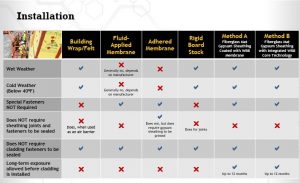
Stucco
Stucco and other commercial building finishes may require metal lath fasteners, so selecting the right sheathing is essential. If magnesium oxide (MgO) boards are used, chemical compatibility with fasteners could become an issue. A five-year study out of Denmark, where MgO boards had been widely used, found salts in the magnesium absorbed ambient humidity, causing fastener corrosion and moisture damage to wood-framing materials. While MgO sheathings offer fire-resistance at a lower cost than gypsum, the potential corrosion risk could cause more expensive problems down the roads.
Masonry
Brick and cultured stone are popular options for building façades, but they are also highly absorbent. While building cladding is meant to be the first defense against bulk water intrusion, these material selections all but ensure water will penetrate the cladding. In these situations, designers must be confident their selected sheathing and WRB will drain and dry effectively.
When building wraps are selected as the WRB of choice, penetrations and perforations in the material become the issue. As building science expert Joseph Lstiburek explains, moisture intrusion through fastener penetrations is fine, as long as the wall can handle (i.e. thoroughly dry) the amount of moisture that gets through. If papers tear because of the wind, insufficient folding around punched openings, or other issues, the amount of moisture infiltrating the wrap could overwhelm the sheathing’s drying capabilities.
Simplification in a single product
Gypsum-integrated WRB-AB sheathing systems combine water and air control into one system that will work behind almost all types of cladding, provided wall assembly designers have taken effective steps toward good water management. Direct-applied systems would be discouraged without the inclusion of a drainage cavity.
With extensive testing regarding permeability and wind-driven rain, manufacturers have calculated air- and water-barrier qualities that will work successfully with a range of cladding options, thereby eliminating the additional labor and supplies needed to install multiple layers. Third-party testing has been performed to evaluate a variety of performance characteristics of gypsum-integrated WRB-AB materials such as:
- adhesive compatibility, according to ASTM C297, Standard Test Method for Flatwise Tensile Strength of Sandwich Constructions;
- drainage capability, per ASTM E2273, Standard Test Method for Determining the Drainage Efficiency of Exterior Insulation and Finish Systems (EIFS) Clad Wall Assemblies, with adhesively attached claddings such as EIFS;
- effectiveness of integrated WRB sheathings when penetrated by mechanical means of cladding attachment, including multiple types of rainscreen bracket and clip systems, in wind-drive rain events, according to ASTM E331, Standard Test Method for Water Penetration of Exterior Windows, Skylights, Doors, and Curtain Walls by Uniform Static Air Pressure Difference; and
- fastener sealability of the WRB, and ability to hold out water under hydrostatic pressure when the barrier is mechanically penetrated, per ASTM D1970, Standard Specification for Self-adhering Polymer Modified Bituminous Sheet Materials Used as Steep Roofing Underlayment for Ice Dam Protection.
In all cases, integrated WRB sheathings have exceeded code requirements for performance.
Depending on the production process of the integrated materials, the protective WRB-AB layers may be incorporated into the gypsum while the slurry is poured, or applied as a coating to the finished gypsum panels. In both circumstances, the resulting single material eliminates the need for architects or engineers to consider the characteristics of multiple materials and their compatibility with the chosen cladding.
As it is with any building material, proper installation is essential for long-term performance. The gypsum-integrated WRB-AB sheathing panels should be butted tight with a 1.6-mm (1/16-in.) gap and screwed to the framing, according to the fastener schedule provided by the manufacturer. Installers will then need to seal the gaps, seams, and fastener locations using liquid-applied flashing, the type and thickness of which would be specified by the sheathing manufacturer. Depending on the situation, a backer rod might be recommended in some instances, but typically, the liquid flashing will suffice.