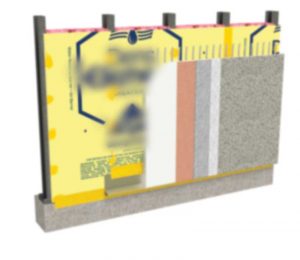
In terms of code-compliance, the Air Barrier Association of America (ABAA) requires membranes factory-bonded to sheathing to display inherent self- or fastener sealability, as outlined in paragraph 7.9 of ASTM D1970. Integral gypsum WRB-AB sheathing boards meet this requirement on their own, so installers can be confident they will not have issues with excess moisture infiltrating fastener penetrations.
The step of sealing gaps and fasteners in a visible way with liquid-applied flashing also gives the sheathing an added element of quality control upon installation. Crew-members and building inspectors can easily see missed areas, unlike with building wraps where incorrect folds or laps might be difficult to spot, or liquid-applied moisture barriers that demand a specific thickness for proper performance. Ease of installation for integrated sheathing leaves installers and building owners confident that they are not creating new opportunities for air or water intrusion before the cladding even goes on.
Installers will also be pleased to hear gypsum-integrated sheathings are compatible with a wide range of climate and weather conditions. As climate zones impact the wall assembly as a whole, integrated sheathings can be used in any region, provided other wall components allow for it. Product limitations will vary by type and manufacturer, but generally the materials can be installed in any weather condition, and can be typically exposed for up to 12 months.
Case study
A North Carolina off-grid property known as Benoit Farms took advantage of gypsum-integrated WRB-AB sheathing to leverage its performance benefits and cladding compatibility. Atlanta-based architecture firm LG Squared was tasked with creating a building that would have reduced energy use while still managing the unpredictable weather of western North Carolina (Climate Zone 4). Dramatic shifts in moisture levels and temperature swings throughout the year, as well as potential forest fires in nearby mountain areas meant the firm needed a sheathing material that could maximize energy efficiency, provide a continuous WRB-AB layer, and protect the building, its occupants, and the surrounding landscape from fire risk.
The integrated sheathing addressed the majority of these concerns with one product and limited trips around the building to install it. The selected wall assembly incorporated a gypsum-integrated WRB-AB sheathing matched with a liquid flashing approved for damp conditions, which sealed the joints, seams, corners, and penetrations. Altogether, this installation created a hydrophobic, monolithic surface to block bulk water, and an airtight building enclosure to achieve energy-efficiency goals, all while allowing for vapor permeability and effective drying and providing fire resistance, as required by the National Fire Protection Association (NFPA) 285, Standard Fire Test Method for Evaluation of Fire Propagation Characteristics of Exterior Wall Assemblies Containing Combustible Components.
With barrier layers fully sealed, the construction team turned its attention to the exterior cladding and aesthetic of the building. The Benoit Farms project called for a layer of ci to achieve its energy-efficiency goals. On top of that, the project called for 20-gauge corrugated steel cladding on the residential building and one barn, and 14-gauge steel on a second barn. The cladding was attached to 20-gauge hat channels and secured through the ci and into 18-gauge metal framing with long roofing screws. Behind the scenes, the gypsum-integrated sheathing provided the air and water barrier, while serving as a rigid substrate for the insulation, and offering structural integrity in the way of shear strength for the wall assembly.
Climate and insulation considerations
Two schools of thought exist around keeping moisture out of buildings, recognizing cladding as the first line of defense. One approach favors wall assemblies—including cladding selection and installation techniques—designed to keep water out altogether. The other method acknowledges water infiltration in some form and quantity is inevitable, and effective moisture management is more important than keeping water out in the first place.
As discussed, many popular cladding options are susceptible to moisture, making the second approach a logical one for commercial builders. So, assuming some water is bound to get behind the cladding, gypsum sheathing is a suitable starting point. All gypsum sheathing is vapor permeable and has the capacity to retain its integrity even as it moves through wetting and drying cycles. In selecting a gypsum-integrated WRB-AB sheathing, designers benefit from this quality, as well as the consistency of a known permeability level that will not be changed by the addition of separate control layers. For example, an integrated sheathing rated at 25 perms will retain that rating on installation because it already accounts for the permeability of the WRB-AB. This is in contrast to a non-integrated sheathing whose permeability changes depending on the control layers applied.
However, the issue is complicated by the widespread use of continuous insulation code requirements on commercial buildings. Depending on the type of insulation and its installation—directly up against the WRB-AB layer, or within the cladding installation framing—the location of the drainage plane and drying capabilities of the wall assembly may change.
For example, in a cold climate, designers may choose an integrated WRB-AB sheathing, followed by mineral wool ci, and an air gap between the insulation and their cladding of choice. This wall assembly should dry well to the outside with the cladding spaced off insulation. However, if a foil-faced polyisocyanurate (ISO) ci is used, it would not dry well to the outside. Pressed up against the WRB-AB layer, the ISO would stop movement of moisture at its surface, and designers have to provide a drainage cavity.