By Matt Cornett, AIA, LEED AP, CDT, CCS, CCCA
Most technical specification template sections are available through software programs, but what if a template does not exist for a particular product or assembly? The following article outlines some of the steps to take when creating a spec from scratch.
Step 1 – Is the product or assembly similar to another one that it can be added to? For example, if there was a special treatment process required for glass, does it need to be its own spec section or can it be incorporated into the glazing specification? This is particularly applicable to small items or ones with limited scope.
Step 2 – Is there a manufacturer or fabricator with a three-part guide spec? Do they have product cuts, sample shop drawings, installation instructions, etc.?
Step 3 – Is the product or assembly similar to another item for which a standard spec template exists? If so, it can be used as a framework to create the new section. Many of the articles in parts one and three can potentially be used.
Step 4 – Is there a trade organization involved in the particular product or assembly? If so, it is advisable to contact them for assistance. They have a vested interest in the success of the product or assembly and are usually willing to help.
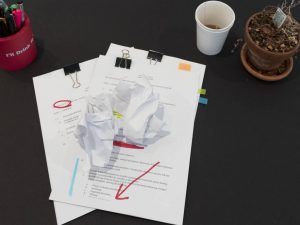
Photo © Jessica Warren. Photo courtesy Gensler
Step 5 – Are there testing organizations, such as ASTM, offering performance criteria for the product or assembly? This is one of the best chances to getting a spec that can be competitively bid, but also have enforceable standards. It is important to be careful and not list test criteria inappropriate for the particular product or assembly. For example, it would not be correct to detail a water penetration test for a fixed window when an operable window is specified. The latter would not be able to perform as well as a fixed one. The product or assembly would not be able to meet the requirements of the specification.
Step 6 – It is recommended to talk to manufacturers or fabricators, and get as much information from them as possible. Inevitably, one will get a better understanding of all of the products or assemblies by talking to multiple representatives. It is like getting a second or third opinion. Sometimes design professionals may find the product or assembly that they thought was required will not work for the application in question or perhaps there is another more commonly specified product or assembly.
Step 7 – Are there governing codes that need to be followed? For example, if one was specifying a custom guardrail, the code-mandated load requirements for the guardrail must be included in the spec section. If one is able to borrow from another section (see step 3), some of this information may already be in there. It is best to always confirm the requirements with applicable codes.
Step 8 – Are there colleagues either inside or outside your organization who have specified or used similar products or assemblies? What lessons did they learn? Perhaps they already created the spec section from scratch. All one needs to do is review and modify to suit the project requirements. It is recommended to confirm reference standards listed in the spec are still current.
ADDITIONAL TIPS |
1. Identify potential questions as early as possible to get enough time to properly research. It may take time for colleagues, manufacturers, or trade representatives to provide the required information. It also reduces the risk of a key person being out on vacation.
2. Refer to MasterFormat as a checklist for what articles would be applicable and in what location. 3. When reviewing manufacturer-specific literature, be aware of pulling information that is only specific to that company. For example, if one manufacturer calls for a certain thickness in metal, it may not be critical for the overall assembly, but is only available from them. In this case, it would be better to list the performance of the product or assembly rather than the description of the metal thickness. 4. Give the new section its own specific number. Narrow down the appropriate Division (first two identifier numbers). Then find the best category of products or assemblies (third and fourth identifier numbers). Lastly, assign the last two numbers that have not been assigned in MasterFormat. 5. If unsure about the applicability of something taken from a similar section or a manufacturer’s guide spec, it is better to leave it out. Unnecessary requirements confuse and weaken a specification. 6. Get the final draft reviewed internally. Get their feedback and revise as needed. If it is important for them to look at specific articles, it is best to point them out. Most will skim through the document, so it is better to focus their attention on the articles of concern. 7. Think about what specification style (descriptive, reference, performance, proprietary) will work best for the particular product or assembly. It is common to have multiple styles within a spec section. Be careful to not have multiple styles within a particular article. For example, it is not recommended to specify thickness as well as the performance of the metal. The potential for conflict would increase. |
Conclusion
Creating a spec section from scratch is not only achievable, but also an interesting learning experience. The above steps are what this author uses as a checklist, and are the basics. The reader may have other ones to add as he/she works through writing from scratch.
The opinions expressed in Specifications are based on the author’s experiences and do not necessarily reflect those of The Construction Specifier or CSI.
Matt Cornett, AIA, LEED AP BD+C, CDT, CCS, CCCA, is a senior project architect and technical director at Gensler in the Morristown New Jersey office. He joined the firm in 2012. He has more than 20 years of experience working on a variety of different building types. Cornett holds a bachelor of architecture degree from Temple University. He can be reached at matt_cornett@gensler.com.