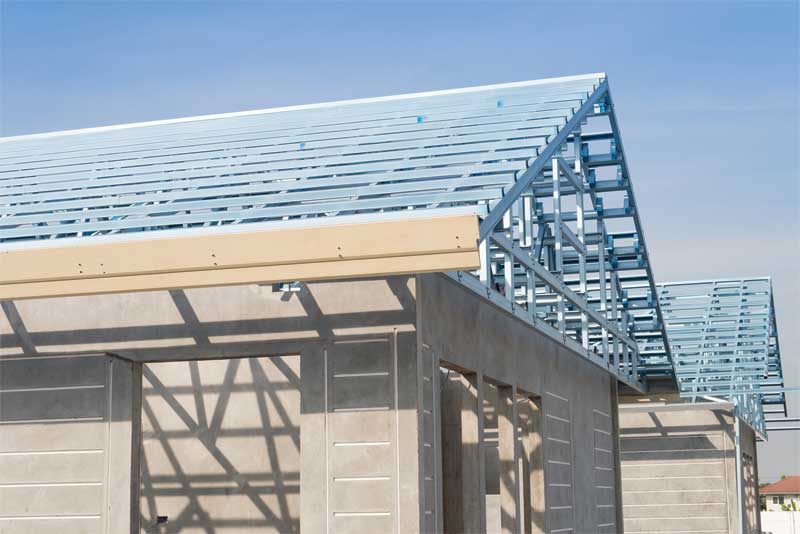
by Gary W. Dallin, P.Eng., and Frank E. Goodwin
Galvanized sheet is used in many industries, including construction, automotive, appliance, electrical hardware, drainage, and HVAC. While there is much information about the corrosion rate of zinc in the myriad environments where this product is used, the specified zinc coating mass is sometimes not suited for the end use. (For more, refer to Corrosion and Electrochemistry of Zinc by X.G. Zhang [Plenum Press, 1996] and Corrosion Resistance of Zinc and Zinc Alloys by F.C. Porter [Marcel Dekker, Inc., 1994].) This may be because corrosion principles are not understood, or a low coating mass is ordered to reduce purchase costs. Early failure can result if coatings are too thin for the application.
Architects and designers of products made from galvanized sheet must know the corrosion severity of the service environment, the design life of the product, and what constitutes a failure to wisely decide on the required zinc coating mass. Questions to be answered include:
- Is it an outdoor or indoor environment?
- Will the product be exposed or sheltered from the weather?
- What are the expected times/duration of wetness?
- Is exposure to chlorides, sulfates, and nitrates involved?
- Are local microclimates (e.g. heavy industry) a factor?
- For indoor applications, will the environment be controlled?
- In the case of buildings, is animal confinement, an indoor pool, or some other moisture/high-humidity source involved?
- Do all parties understand the expected service life and what will be considered a failure (e.g. first appearance of red rust or perforation of the steel substrate)?
- What will be the consequences of failure?
Once all questions have been answered, the corrosion rate of the zinc can be estimated. Combined with the required design life, the minimum coating mass needed can be calculated. For example, design life of 40 years multiplied by corrosion rate of 0.5 microns (μm) per year equals a required coating thickness of 20 μm.
Determining the required coating mass for a given product is therefore not generally a difficult task since the service life of a galvanized coating is a linear function of the environment in which it is placed. However, due to cost reduction requests from users of galvanized sheet, there is growing demand to produce thinner zinc coatings. (For more, refer to “Review on Wiping: A Key Process Limiting CGL Productivity,” by F.E. Goodwin and M. Dubois, presented at the June 2011 Galvatech conference in Genoa, Italy.) This is sometimes at odds with the capability of zinc to meet the service life needed for the intended environment. While many products do not need thick zinc coatings due to benign service conditions or short one-time usage, some thin zinc coatings are applied on end products where early failure is guaranteed. Such applications are a waste of steel substrate, which would have a much longer service life if applied with a thicker zinc coating. It is quite likely false economy, as it will not minimize life-cycle costs (i.e. an alternative with a higher initial cost may be economically justified by reductions in future costs). (For more, refer ASTM A903-09, Standard Practice for Life-Cycle Cost Analysis of Corrugated Metal Pipe Used for Culverts, Storm Sewers, and Other Buried Conduits.)
Continuously galvanized steel sheet is produced on coating lines using gas wiping to remove the excess liquid zinc drawn up from the molten bath by the moving strip. Gas wiping is an efficient process that has been used for many decades and is now at the stage where it can closely control the final coating thickness at line speeds from 50 to 200 m (164 to 656 ft)/min with low maintenance and reasonable investment costs. To produce thinner coatings, though, gas pressure must be increased, and the gas knives moved closer to the moving strip, which can rapidly bring the process near its operational limits. In these cases, line speed must be reduced to achieve a thinner coating. Even then, each coating line has a zinc thickness below which it is physically not possible to wipe. Needing to run slower than rated capacity lowers line productivity and increases operational costs. (For more, read the paper, “Challenges in the Production of Thin Coatings at High Line Speed,” by M. Dubois, et al, presented at the November 2009 Asia–Pacific Galvanizing Conference in Jeju, Korea.) Purchasers expect thinner coatings will reduce the product price, but in fact, the production cost may increase.
The optimal coating mass for a particular product made from galvanized sheet is therefore a balance between the required service life, and the ability of a zinc coating line to produce coating mass at a reasonable cost. If a thin coating is the right product for a particular end use, then the selling price may have to be higher to offset lower coating line productivity, or it may be cheaper to apply more zinc than required. These considerations must be taken into account by the buyer.