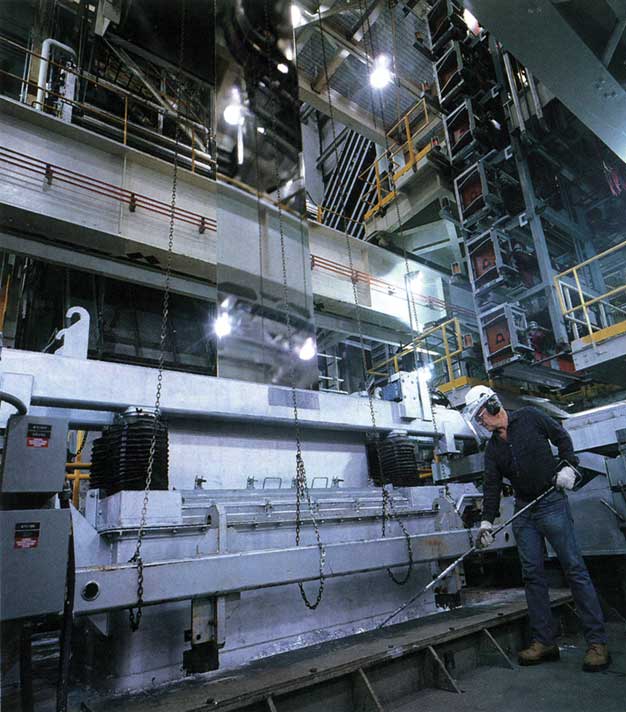
Images courtesy The International Zinc Association (IZA) – GalvInfo Center
Coating thickness designation systems
Most global standards for galvanized sheet, including ASTM International, do not directly use thickness to specify zinc coatings. It is very difficult and expensive to directly and accurately measure the thickness of zinc on coated sheet, as the coating is usually a small fraction of the total coated sheet thickness. In the case of a single coil of galvanized sheet, if thickness is measured manually (and even if accurately done), it is but one very small point on a large surface area, with no assurance the result is representative of the overall coil. A more representative method is to use a destructive, weigh-strip-weigh technique to measure all the zinc on a larger surface area of sheet. This is the main reason galvanized sheet standards specify the coating in terms of mass (weight) per unit area.
The industry does use expensive X-ray and radioisotope fluorescence devices, both on- and off-line, for directly sensing zinc thickness. This equipment requires considerable expertise to operate. On-line units continuously measure the coating thickness as the strip passes by. However, they must regularly be calibrated via the weigh-strip-weigh technique. Further, the real-time results provided are mathematically converted to mass per unit area for purposes of assessing compliance with ASTM and other specifications.
Service life data
In the atmosphere, the corrosion rate of a zinc coating varies widely depending on many environmental factors. For example, “time of wetness” is an important issue affecting corrosion rate (e.g. outdoor applications in a dry climate like Dubai are very different from locations experiencing high annual rainfall or extended foggy periods). Also, the presence of impurities such as sulfates, chlorides, and nitrates can dramatically affect corrosion rate. The presence of these compounds is quite often a function of localized microclimates (e.g. heavy industry and salt spray from major roadways or a sea coast).
Figure 1 shows calculated corrosion rates for six different North American cities in each of the five climate categories. The corrosion rates shown are estimates based on models using data from environmental databases. The calculated corrosion rates used to generate this chart are averages for the six cities. Six common coating mass “bars,” per ASTM A653/A653M, Standard Specification for Steel Sheet, Zinc-Coated (Galvanized) or Zinc-Iron Alloy-Coated (Galvannealed) by the Hot-Dip Process, have been overlaid on the chart. To determine the corrosion rate for a specific locale, the documented actual environmental data can be entered into the software. (For more, click here.)
Although the corrosion rate can vary considerably depending on local environmental factors, as Figure 1 indicates, the life of a zinc coating is a linear function of coating mass for any specific environment. As is also seen in Figure 1, when the per-side coating thickness is much below 10 mm, outdoor service life is less than 10 years, making the use of such thin coatings outdoors an unwise choice.
Note the zinc corrosion data given in Figure 1 is from after circa 1975, when aggressive pollutants such as sulfur dioxide began to decline from their higher levels of the mid-20th century. The service life of galvanized sheet in an urban industrial area is now longer than it was 40 to 60 years ago. On the other hand, corrosion rates in marine environments have not changed much since the rate of zinc loss is governed more by the amount of deposited sea salt than airborne pollutants.
Design vis-à-vis service conditions
“Mistakes in plant design are the most frequently cited (58 percent) cause of corrosion failure in chemical-process industries.” (Corrosion Control by S.A. Bradford, published in 1993 by Van Nostrand Reinhold International [UK].)
While this quote does not refer directly to products manufactured with galvanized sheet, design plays just as important a role in their corrosion failures.
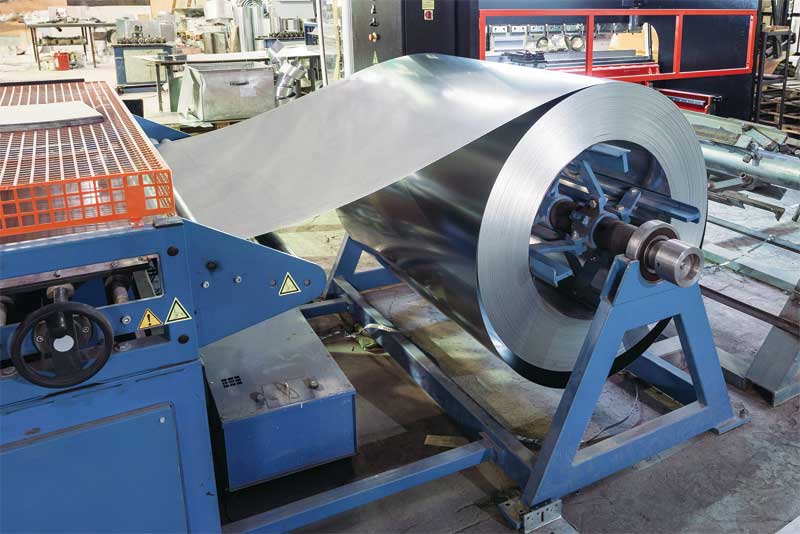
Photos © BigStockPhoto.com
A number of general principles are necessary for a successful design. Those most applicable to products made with galvanized sheet are:
- minimize attack time;
- restrict galvanic cells;
- protect against environmental cells; and
- design for inspection and maintenance.
As mentioned earlier, zinc coatings corrode uniformly at known rates in the atmosphere, and most other environments, so the coating thickness needed to last for the design life of an application can easily be calculated. The best designs take advantage of the uniform corrosion of zinc, avoiding situations causing accelerated, localized attacks.
When zinc is exposed to wet/dry weather cycles it forms a very thin, protective zinc oxycarbonate patina. (For more, click here.) However, a very small amount of zinc is dissolved by rainwater and removed during each wetting event. In designing a structure, it is important to ensure the entire exposed surface (e.g. roof elevation and side wall) always “sees” the same weather as uniformly as possible across the entire surface area. If some portion of a roof receives extra water, draining from some higher, non-zinc coated surface, then the extra water takes its share of zinc (in addition to the amount taken by the rain that fell directly on it). The area of impingement has its zinc coating removed at a higher rate.
In designing a building subject to weather, avoid configurations where water drains incompletely and/or pools. When subjected to long periods of wetness, the protective zinc oxycarbonate patina layer breaks down, increasing the zinc corrosion rate. Well-designed structures clad with galvanized sheet have good drainage and dry uniformly and quickly after a rain event.
Some soils are very corrosive to zinc. To avoid problems, design galvanized sheet on buildings away from the ground.
Galvanized sheet used to clad some commercial and industrial buildings, and many farm buildings, is sometimes the only separation between the inside and outside “climate” (i.e. there is no inner wall or ceiling structures separated from the outer wall by insulation). This is the case in many animal confinement buildings, where it can become warm and humid inside. In the winter, condensation can form on the inside of the wall and roof panels. If ventilation is poor, condensate can be present for long periods, accelerating corrosion of zinc coatings. Animal waste decomposition products (e.g. sulfides, ureas, and amines) become dissolved in the condensate, adding to the corrosivity of the environment. (For more, refer to the U.S. Steel technical bulletin TBP 2005.2, “The use of steel building panels for animal confinement.”) The solution is to have the building design include insulation with adequate ventilation to both remove gaseous decomposition products and prevent moisture buildup and condensation inside the structure.
Sometimes, even with the right coating mass, problems can arise. Using a coating thinner than required to save some material costs upfront can only compound design errors, bringing on an even earlier failure. Figure 2 shows GalvInfo Center’s recommended minimum coating mass to be used for a variety of common galvanized sheet applications. (For more, click here.)