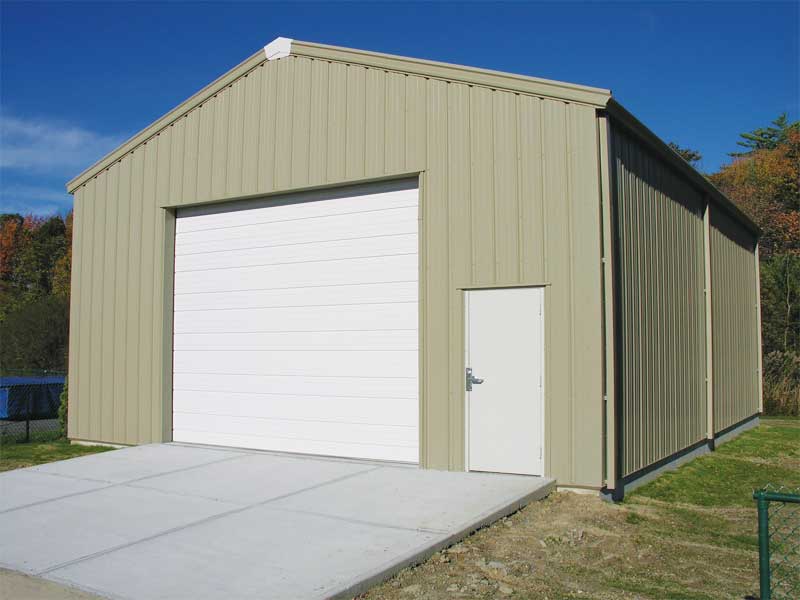
Gas wiping process
The gas wiping process used to apply zinc coatings on continuous coating lines has many practical advantages. It is simple, requires minimal maintenance, has a low operational cost and low energy requirements, and a large process window. The sheet vertically exits the bath at high speeds, dragging out more zinc than needed for the coating. Gas knives employ low-pressure/high-volume gas streams (almost always air) impinging against both sheet surfaces. The gas flows through two knife boxes positioned parallel and adjacent to each side of the strip. It escapes through precisely machined slot openings placed about 10 to 12 mm (395 to 470 mils) from the traveling strip. The gas jet acts as a knife, stripping the excess molten zinc and forcing it back down to the coating bath. For line speeds over 100 m/min and coating thicknesses below 20 μm, the final thickness depends linearly on the nozzle-to-strip distance when the distance is more than seven times the nozzle opening.
As a result of the limited effect of the distance when it is less than seven times the nozzle gap, wiping infinitely close will not lead to an infinitely thin coating.
The nozzle-to-strip distance cannot be kept safely below 7 to 8 mm (275 to 315 mils), since the risk is too high of the strip touching the nozzles due to strip vibration and/or not perfectly flat sheet.
When the nozzle-to-strip distance is less than six to seven times the nozzle opening, the coating thickness will decrease only slightly. At less than below this wiping distance it is generally accepted the risk of the knives touching the strip is too high, especially on wide material, and the minimum nozzle opening should be 0.8 mm (30 mils).
Thin coatings on thin sheet are expensive to produce. The present best per-side industrial practice is about 35 g/m2 (5 mm). (For more, consult “Maximum Line Speed Limit with a Minimum Coating Weight, Where is the Limit?” by M. Dubois and J. Callegari, presented at the June 2011 Galvatech conference in Genoa, Italy.) Using the best wiping practice, 50 g/m2 becomes cheaper than 35 g/m2 on thin sheets due to the needed reduction in line speed to reach thin layers. The minimum galvanizing cost is in the range of 52 to 72 g/m2/side.
As coatings on thin sheet are more expensive to produce, it is economical to give away extra zinc to increase line productivity. It is in the best interests of continuous galvanizing lines to develop a cost map for the particulars of each line. Marketing staff would then know the sheet thickness range of when it makes sense to offer a 35 g/m2 (5 mm) per side coating vs. when to decline such orders or add a surcharge to offset the reduced productivity.
There are also a number of quality issues associated with producing thin zinc coatings while running at high line speeds, such as bright spots and an edge effect due to accumulation of oxides.
The gas wiping process also has a physical limit related to a splashing phenomenon. The air knife can become inefficient, requiring an immediate line slow down to allow the exploding back flow to remain on the sheet.
Narrow nozzle openings are very sensitive to dust, zinc splashes, and scratches, all of which can lead to jet (blower) lines. In practice, an opening below 0.8 mm is very difficult to operate.
The amount of dross (floating zinc oxide [ZnO] scum) produced is also a large concern when producing thin coatings at high line speed. When total gas flow from the knives is too high, the level of dross becomes unacceptable. In the case of zinc containing 0.25 percent aluminum run at 130 m/min it was observed the dross created was 25 to 30 g/m2 for both sides. At 80 m/min the amount of dross dropped to 12 to 15 g/m2. Dross must be removed during top drossing of the bath to avoid entrainment in the coating and surface defects on the final product.
Pre-painted galvanized sheet
Coil-coated steel sheets are widely used in construction, automotive, and appliance industries. Their superior corrosion stability is explained by the synergistic protection provided by metallic and organic coatings. (Note: For more, read “Effect of steel and coating thickness on edge creep of coil coated materials” by T. Prosek, et al. presented at the 2015 Galvatech conference in Toronto, Canada.) Besides defects such as scratches occurring during transport, processing, installation, and product service life, the cut edges of pre-painted panels expose the steel and are usually not treated. Paint delamination at cut edges is a principle reason for the failure of coil-coated steel sheets.
The aim of the study in reference was to investigate the role of the metallic coating thickness on long-term cut edge protection of coil-coated products. (See previous note.) Paint delamination from cut edges of coil-coated materials was followed as a function of exposure time at a marine test site for 17 hot-dip galvanized materials differing in the thickness of zinc coating (7 to 20 μm) and steel substrate (0.2 to 2.5 mm [8 to 100 mils]). Results are shown in Figure 3.
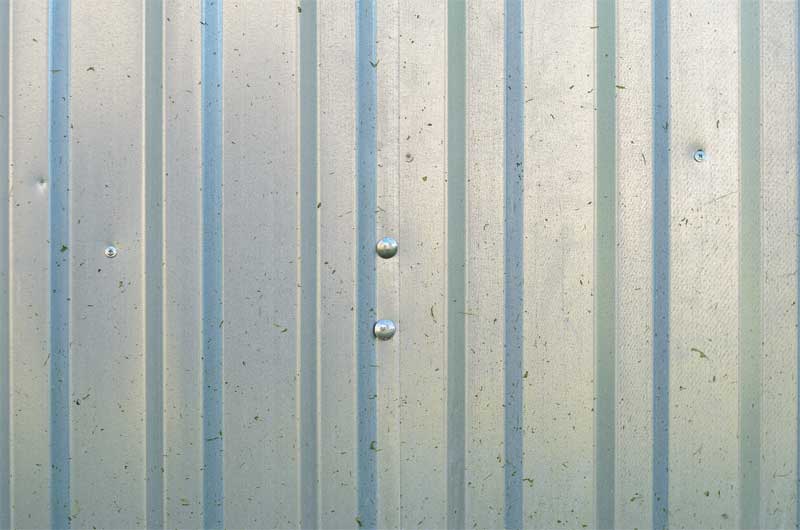
The study concluded edge creep (i.e. corrosion under the paint creeping in from cut edges) increases with decreasing zinc thickness and increasing steel thickness. For steel substrates over 0.75 mm (30 mils), any reduction in coating thickness below Z275 (20 μm) leads to an accelerating drop in service life due to edge creep. (Note: The “Z” means the coating is galvanized [zinc] and the number refers to the mass of zinc on the surface of the steel sheet in g/m2 [e.g. Z275 = 275 g/m2 total both sides]). For steel thickness less than 0.75 mm, the effect of zinc thickness in protecting against edge creep was not so pronounced.
In the case of pre-painted galvanized sheet, zinc supports the paint, protecting against under-film corrosion. The thicker the zinc the slower the under-film corrosion proceeds, so the protection time is longer. This is even more the case as the steel substrate thickness decreases. As paint costs from five to 25 times more than Z275 coatings per unit area, using thinner zinc coatings in exposed environments is an ineffective and wasteful use of resources, particularly in cases where the steel thickness is above 0.75 mm. Once the zinc layer is gone, the paint is of little value in protecting the steel.
These field performance results indicate a Z275 coating is strongly advised for all exterior pre-painted sheet applications, except for the potential use of Z180 in cases where the climate is dry and the environment no more aggressive than urban.
Figure 4 shows recommended minimum coating mass to be used for a variety of common pre-painted galvanized sheet applications.
Conclusion
The coating thickness of galvanized sheet determines its life. To select the proper coating mass, it is important to know and understand the following:
- the expected service life of the end use;
- what defines a failure;
- the particulars of the service environment and the coating mass needed to meet the service life;
- selection of coating designations too thin for the application will result in reduced corrosion performance of the product (in an almost linear relationship);
- the coating mass having the minimum production cost is somewhere in the range of 52 to 72 g/m2/side for zinc coatings; and
- for pre-painted sheet, the importance of enough zinc being present on the substrate to minimize under-film corrosion and outlast the expensive paint coating layers.
When deciding on the required coating mass there are a number of considerations. Designers should use the wealth of published knowledge on the corrosion rate of zinc in most environments. When this is not taken into account, or ignored, it is false economy to sacrifice service life to save the relatively small upfront zinc cost of a too-thin coating mass. Certainly, in the authors’ experience using less than 120 g/m2 for outdoor applications is unwise, both from a product life-cycle cost and a sustainability standpoint. Ordering thinner coatings decreases coating productivity and increases costs, as producers may ask a higher selling price. Also, thin, hot-dip zinc coatings can sometimes be impossible to produce. In the case of pre-painted galvanized sheet, zinc supports the paint, protecting against under-film corrosion, so the zinc coating should be thick enough to outlast the life of the paint cover.
Aside from the steel substrate, zinc is the single largest cost component of galvanized sheet. It is understandable why the marketplace wants to use thinner zinc coatings. Architects and specifiers can use this article to better understand how service environment, using the correct coating mass, and proper design can minimize corrosion, lengthen service life, and reduce life-cycle costs.
Gary Dallin, P.Eng., is director of the GalvInfo Center, a program of the International Zinc Association (IZA). Previously, he was employed as a metallurgist in the Canadian steel industry. Dallin has 48 years of experience with galvanized and pre-painted steel sheet products, is a registered Professional Engineer in Ontario, and is active on ASTM International Committee A05 on metallic-coated steel products. Dallin can be contacted at info@galvinfo.com.
Frank E. Goodwin is executive vice-president of International Lead Zinc Research Organization (ILZRO) and also director of technology and market development of International Zinc Association (IZA). Goodwin joined ILZRO in 1982 as manager of program development after serving as assistant director of product and process development at Chromalloy Research and Technology Division in Orangeburg, New York. Following his appointment as ILZRO’s manager of metallurgy and program development in 1984, he was promoted to vice-president of materials science in 1986. He holds a master’s degree and a PhD in materials engineering from the Massachusetts Institute of Technology in Cambridge, Massachusetts. Goodwin is also the author of several national and foreign patents as well as numerous articles and book contributions. He can be reached at fgoodwin@zinc.org.